- Client: Olympic Delivery Authority (ODA)
- Sectors: Major Projects, Leisure
- Size: 20,500m2
- Location: London
- Services: McAlpine Design Group, Pre-Construction, Construction Support
- Completion date: 2011
Low-carbon stadium a showcase for engineering
A case study in innovation, collaboration and adding social value, the Olympic Stadium captured the pride of a nation.
We were proud to be selected as the main contractor for London's Olympic Stadium.
We were eager to create a venue that would not only capture the world’s attention, but would showcase innovative design, sustainability, engineering excellence and collaborative working.
Our ability to ‘embrace the temporary’ was critical in delivering an 80,000-seat stadium, that could be turned into a 25,000-seat athletics venue after 2012.
The result was a lean, efficient and highly accessible venue, bringing spectators closer to the action than in previous Games.
The venue's compact size reduced costs, accelerated programme and helped meet our client’s sustainability aspirations. We sped up construction through creative design and developed an alternative roof solution which reduced the amount of steel required.
Delivered early, under budget and with an exemplary safety record, the stadium showcases the power of integrated working and leaves an inspiring legacy.
Summary
Record-breaking
Containing around 10,000 tonnes of steel the venue is the lightest Olympic Stadium to date.
Sustainability
We exceeded our client’s targets on sustainability, carbon emissions, waste segregation, equality and inclusion, recycled content and water. Because of the stadium’s compact design, far less energy was needed to manufacture its individual elements than previous Olympic stadia.
Successful collaboration
Thanks to close teamwork, we delivered the stadium more than two months early and under budget. Our project partners included architect Populous and structural engineer Buro Happold.
Safety focus
Extensive workforce training and engagement resulted in exemplary safety standards.
Lightweight strength
The combined weight of the sports lighting towers on the cable net roof was a first in stadium design.
Lasting community legacy
To boost education and employment in the area, we worked with the local community to provide skills, training, engagement and work opportunities.
Design efficiency
Through applying smart design, we reduced the time from end-concept to start of construction by 12 months. This was achieved through creating a repetitive design, which maximised prefabrication, minimised components and simplified connections.
Our project team’s alternative proposal for a lightweight cable net roof was the most sustainable option, using only half the steel of a standard cantilever design.

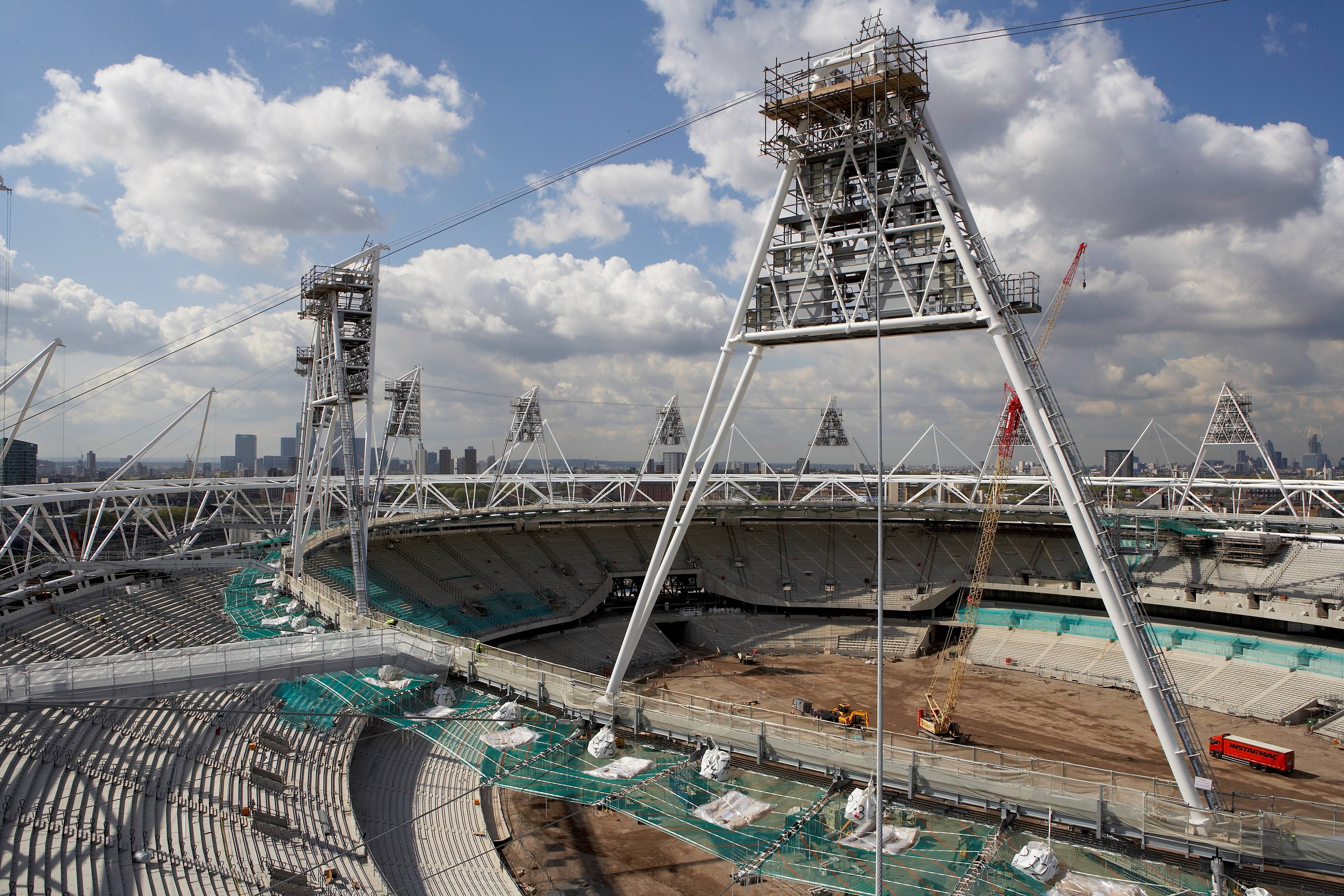
Raising the roof
Erecting the cable net roof and sports lighting towers were major project challenges. The entire process was designed to minimise work at height.
Precision fabrication and installation ensured the 28 steel sections forming the roof’s outer compression truss fitted perfectly.
Then we laid the inner tension ring on a scaffold, which was custom-made by our in-house design team to run around the inside of the bowl. From here, the ring was lifted 40m into place using computer-controlled jacks.
The 14 sports lighting towers were constructed on the playing field. Equipment and circuits were tested at ground level before the rigs were lifted onto the tension ring and secured with a secondary system of cables.
With each tower weighing 35 tonnes, their combined weight on the edge of a cable net roof was a first in stadium design.
Awards
-
Considerate Constructors Scheme Awards
National site awards 2011 & 2012 - Gold
-
Secured by Design certification
First UK stadium to receive the Secured by Design certification for the measures taken to reduce crime and anti-social behaviour.