- Client: Unipres UK
- Sector: Industrial
- Value: £15m
- Size: 50,000m2
- Region: North East
Expansion to Nissan’s component manufacturer Unipres, Sunderland
Sustainable construction and a close working client relationship were key in delivering the expansion of Unipres’ live production facility in Sunderland.
A partnership lasting over 25-years, we continue expanding Unipres’ manufacturing site to provide architectural and engineering excellence to the 50,000m2 industrial facility.
We have undertaken numerous projects for Unipres UK, transforming the vehicle components manufacturer’s Sunderland site.
Over the past 25 years, we have significantly contributed to the conversion of a once green field into an industrial production facility that now covers some 50,000m2.
The latest expansion project delivered by the company is designed to enable Unipres to increase capacity and fulfil manufacturing orders for parts to be used in ‘eco-cars’ such as the Nissan Leaf.
Project summary
Expansion to Unipres manufacturing facility, Sunderland
Our in-house Design Group provided architectural and structural engineering services on the project, including the design and construction of a 7,650m2 assembly shop and a 5,175m2 press shop. Key elements involved the construction of a concrete press pit and tunnels, requiring a sheet piled cofferdam 30m long, 9m wide and 7.5m deep.
The close working relationship built up with Unipres over previous phases ensured our in-depth understanding of the production demands of our client, with the site remaining live throughout the industrial expansion.
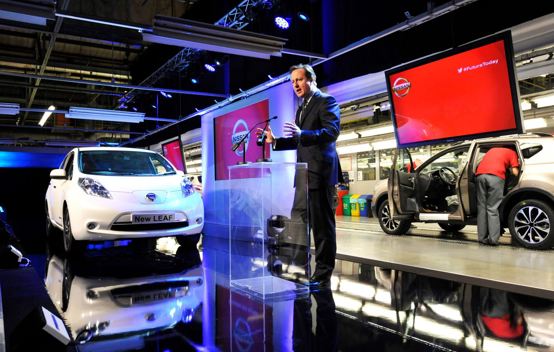
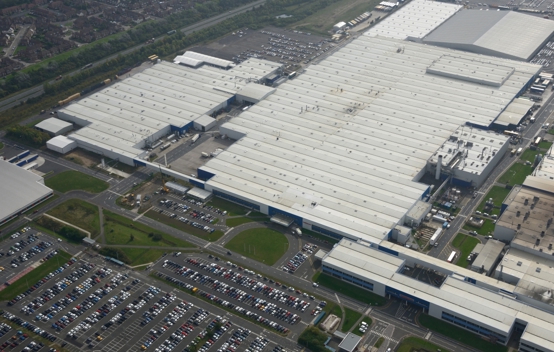
We were able to develop the design and programme the works to minimise disruption to the manufacturing line. Unipres continued operating 24 hours a day and seven days a week, supplying components to global clients such as Nissan.
Throughout our work with Unipres, we were committed to integrating sustainability into various aspects of the industrial expansion.At our suggestion, advanced lighting technology was installed to reduce electrical consumption in the extension by up to 20%, with plans to expand the system throughout the existing factory.
In addition, 4,500m3 of excavated material was tested, cleared and transported under the CL:AIRE protocol; later being reused at one of our adjacent projects.
Our team handed over the project ahead of schedule, the project continues our successful involvement with this specialist manufacturer.
-
Industrial
We build advanced manufacturing plants and vast warehouses, enabling UK industries to adapt to technological changes and meet market demands.
Industrial projects
-
Harbourside Port Talbot development
Harbourside: A benchmark for sustainable construction in Port Talbot
Sectors: IndustrialRegion: Wales -
McLaren Production Centre: Innovation meets efficiency
An example of industrial excellence displaying attention to detail and cutting-edge technology for a high-tech supercar manufacturing facility.
Sectors: IndustrialRegion: South East -
Evolving Nissan’s manufacturing site
Since constructing its original factory in the mid-1980s, we’ve worked closely with the car manufacturer as it has cemented its place in the European market.
Sectors: IndustrialRegion: North East