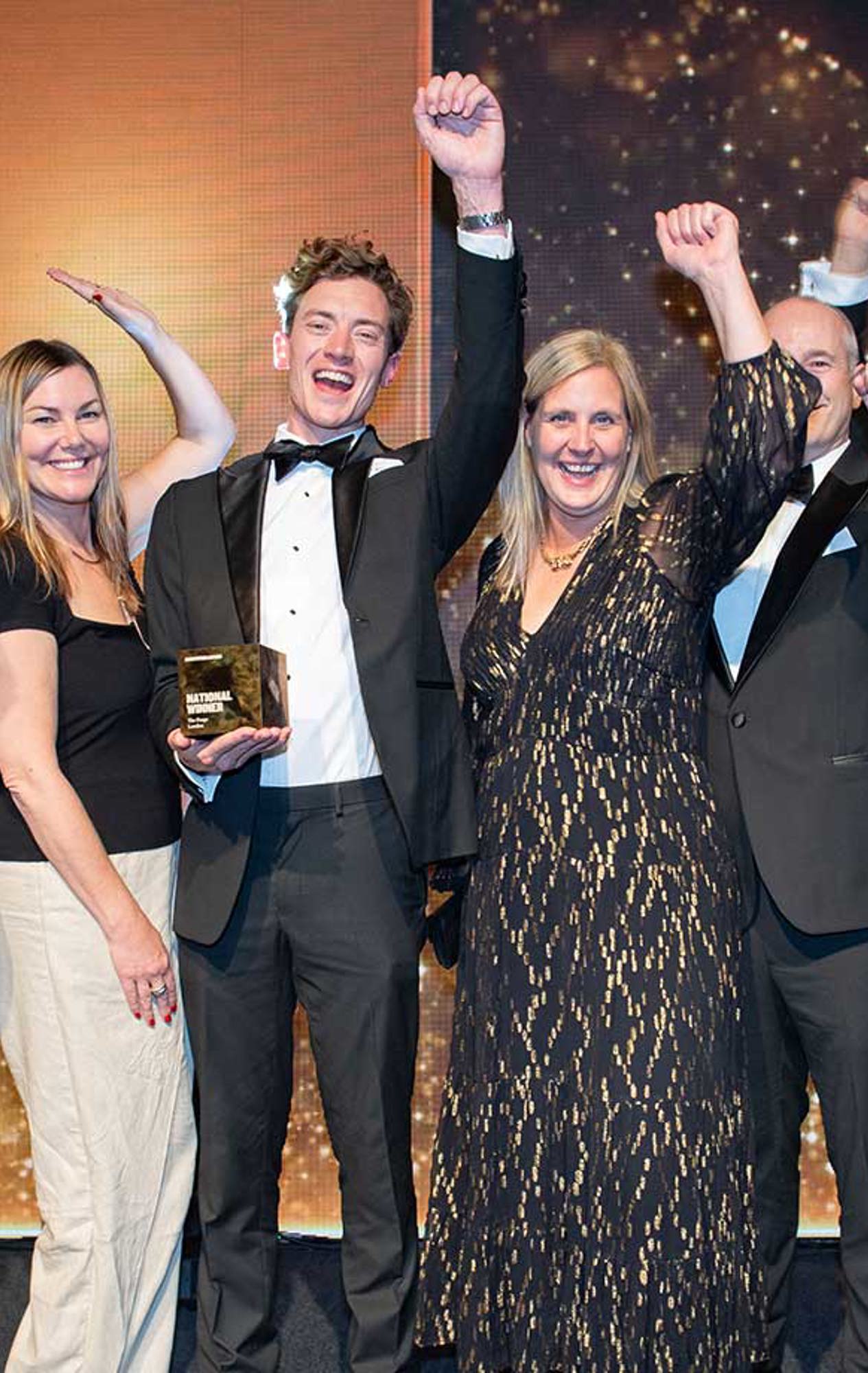
Double honours at the BCO awards
11 Oct 2024The Forge picked up top honours in the Innovation category, whilst 1 New Park Square (Edinburgh Park) was named winner of the Commercial Workplace Award.
We’re helping deliver The Forge, a project that’s designed to change the face of construction.
At The Forge, the structural steelwork, temporary works, cladding and on-floor MEP are all standardised, based on a prototype created by client Landsec with their design partners Bryden Wood and manufacturing specialist Easi-Space.
The idea is to demonstrate that a set of standard components can be combined to create a range of customised spaces, saving time and money, improving quality and safety, and reducing waste.
These standard components can then be used on a wide range of construction projects going forward, raising standards across the industry.
Digital construction is playing a key role in our delivery of The Forge. Working closely with the Landsec, we’ve carefully selected a set of digital tools that allow us to capture and use data to reduce programme times, improve quality and deliver best value.
One of these tools, Converge is an innovative digital platform which provides live concrete temperature and strength data via the cloud. IoT temperature sensors embedded in the concrete (pictured right) transmit temperature readings wirelessly to data hubs located on each floor. The technology will be used to inform decision making on site. The Converge software platform uses machine learning to predict the concrete strength gain from the temperature changes in the concrete. In effect when combined with the BIM model data it creates a digital twin of the concreting process. The accurate strength prediction will allow the project team to plan ahead with confidence and allow the temporary works to be struck faster avoiding delays on site.
Another tool we’re using, Disperse, creates interactive 3D models of the site that provide a 360-degree ‘Street View’ around the project. Produced weekly, these 3D scans act as both an up-to-date visual digital twin, allowing details of the build to be viewed remotely, and a searchable digital archive which tracks progress and key changes throughout the job.
We are trialling the use of QR codes to track the progress of materials throughout the build. By scanning items on arrival and then again when in their final position, we can speed up the traditional reporting process and provide sub-contractors with a live analysis of progress on site.
We are also using digital tools to help us keep on top of the sustainability targets Landsec have set, and collect data to help create industry benchmarks on waste management. One of these, Qflow, uses a unique combination of Artificial Intelligence (AI) and Machine Learning (ML) to automate data capture at the site gate and provide analysis to help drive both commercial and carbon savings and reduce the risk of failing to meet the waste transfer regulations.
Josh Harding, Digital Construction Manager at Sir Robert McAlpine, is going over and above the usual day-to-day duties of his role to deliver on Landsec’s aspiration to raise the bar on digital with this project.
A great example of this has been his work to create a digital dashboard (pictured below) collating all the key sources of data in one place, providing everyone in the team with easy access to up to date information and enabling managers to make informed, data led decisions to direct the works on site.
Padraig Delaney, London Regional Manager for Digital Construction at Sir Robert McAlpine, sees The Forge as a model for how we can deliver future projects:
The innovation-led approach taken by Landsec has allowed us to push the boundaries with our use of technology. The more data we have, the better our decision making. But it’s also important we have the right tools to help us get the most from the data. By driving these digital solutions, as we have done at The Forge, we’re transforming the way we deliver future projects, identifying the value to each stakeholder and ultimately providing the best value for our clients.
Our and Landsec’s ambition is to make the Forge the UK's first net zero carbon commercial building: specifically, the first UK office building that is net zero carbon in both construction and operation according to the UK Green Building Council's net zero carbon buildings framework. They're also aiming for BREEAM Excellent; and the building's designed in such a way that they'll be able to seek WELL accreditation later on, once it's fully fitted out.
The P-DfMA approach we're following on the project comes with a host of sustainability benefits: most significantly, it makes material use a lot more efficient, so less is wasted. Already embodied carbon in the building has been reduced by 19.4%, thanks partly to a concrete mix containing 40% GGBS, a highly sustainable cement replacement. And, unusually for an office development, both steel and concrete take a structural role in the building's superstructure, with a prefabricated steel frame and concrete filled Comflor beams, poured in situ replacing the secondary steelwork. This hybrid superstructure combines the benefits of the reduced weight and speed of erection of steel frame and the cost effectiveness and visual aesthetic of concrete. It uses less material than traditional methods and is built to higher tolerances. The slabs are poured using reusable temporary formwork, eliminating the need for permanent secondary steelwork so that, again, fewer materials are needed to construct the building.
The propping system that's been developed to support the temporary works before, during and after the concrete pour is also reusable: the props are removed about ten days after a pour and used on the floors above. The innovative diagonal design of the props takes the load from the concrete above through the building frame, so there's no need for traditional back-propping – which means that the slabs below are freed up for more construction work.
With four other major construction projects going on in the area, and concerned neighbours overlooking the site, we're working hard to build good relationships in the community. We've joined the Bankside Consortium, a forum for all the contractors operating in the area to discuss how we can reduce the impact of what we're doing on local people and the environment.
Neil Pennell, Head of Design Innovation and Property Solutions at Landsec, comments on the impact The Forge is set to have on the industry:
“The Forge is setting new industry standards for sustainable and cost-effective construction. The pioneering approach we have taken to design and construction will transform how offices are built in the future. Our experiences over the next year at the capital’s most innovative construction site will shape the way we approach future projects and change the industry for the better.
Sir Robert McAlpine’s team of experts have already demonstrated how passionate they are about The Forge and bringing our vision to life. I look forward to continuing our partnership with them, on this very exciting project.”
The innovation on the project is wide ranging with a real drive to be a catalyst for change in the industry. We are delivering the project as the Manufacturing and Assembly Managers (MAM) in a joint venture with Mace, so that the client gets the combined benefit of two forward looking industry leading construction companies to deliver what is a disruptive project.
The Forge has been selected by UKRI Innovate UK as a Demonstrator project for the Government's Transforming Construction Challenge, pioneering a Platforms approach for more productive and sustainable automated builds.
All aspects of the project have challenged the industry norm to explore alternative approaches. This includes design and procurement, with the multi-disciplinary input of BWT taking design to RIBA Stage 5 for structural and cladding elements, which have then been procured as separate supply and installation packages.
Richard Sansom, Landsec, Project Manager for The Forge, appreciates the work being done by the team:
“We want to lead the sector in the adoption of new methods and technologies. However, the real value in innovation lies in its practical execution. As with anything being done for the first time there are always going to be challenges along the way but we are in a great position to handle these thanks to the experienced and expert team working with us.”
Success for the project will be the learning that has been achieved and objective measurement of the innovation methods that can be applied on future projects and the wider industry. I feel privileged to be working on a project as forward thinking and innovative as The Forge.
Angela Branch Project Director, Sir Robert McAlpine
The Forge picked up top honours in the Innovation category, whilst 1 New Park Square (Edinburgh Park) was named winner of the Commercial Workplace Award.
Congratulations to the project team on completing the construction of The Forge in London, as Chris Skidmore MP officially opened the building this week.
Tower Works, Morello, Haymarket, Royal Bournemouth Hospital and The Forge are amongst the sites awarded 45/45 in their recent Considerate Construction Scheme (CCS) audits.
Congratulations to Rachael Smith, our Head of HR – Strategy & Transformation, who was named Role Model of the Year at the British Forces in Business Awards 2025.
During Armed Forces Week, we speak to Katy Maloney to understand how our commitment to the Forces community provides essential support for military families.
As we celebrate the beginning of Armed Forces Week 2025, we are thrilled to announce that we have been awarded the Defence Employer Recognition Scheme (ERS) Silver Award.